By Ray Heisey, PE, RRC
Senior Consultant
Metal roof systems are a popular choice for commercial buildings for many reasons: durability, aesthetics, cost-effectiveness, and the availability of options to extend the life of the roof.
If leaks do develop in a metal roof, contractors, manufacturers, and insurance companies often take the approach of suggesting a full recoat or a full tear off and replacement, rather than inspecting and addressing specific issues or defects.
Regardless of the size of the company or the size of the building, Benchmark’s position as an independent third-party roof consultant prioritizes practical options to extend asset life over application of a coating or a full roof replacement whenever possible. Case in point: two very different businesses and two very different issues with their metal roofs. After Benchmark thoroughly inspected the metal roofs, both had the same end result—substantial cost savings for the client and better performing roofs.
Global manufacturer — Michigan
As a current client, the company’s roof assets are well-known to Benchmark. Their campus has two large buildings with metal roofs. After water leaks began occurring regularly in one of the buildings, a contractor/manufacturer had recommended fixing the problem by applying a coating to the entire roof surface. While less expensive than a new roof overlay (estimated at $15 to $20 a square foot) the application of a coating is typically over $5 a square foot—a costly price tag for a building this size.
After a thorough inspection by Benchmark, it was determined that 95% of the roof was in good shape and could last another 15 – 20 years with proper repairs and maintenance. Repairs were recommended for specific areas of the roof to correct the cause of persistent leaking, which included:
- Removing fasteners and some ridge components, resealing, and reinstalling the components with new fasteners.
- Gutters were creating ice damming and leaks along the metal walls. Removing the gutters and installing protective covers directly over the doors and light fixtures eliminated the ice damming.
- Painting rusting pipe flashings that were not leaking, but would have rusted through, causing leaks into the building.
The cost of the recommended repairs to address the specific leak and maintenance issues for the roof: approximately $40,000 – $50,000, saving the client about $700,000.
Regional printing services provider — Iowa
While metal roofs are known for their durability, severe weather can still cause damage, as was the case with a company near Benchmark’s corporate offices in Cedar Rapids, Iowa.
In 2020, a derecho tore through the area, with sustained 140 mph straight line winds which damaged two exposed fastener, ribbed metal roofs on the company’s 45,295 square foot facility, resulting in leaks. Leaks are highly disruptive and damaging to printing operations.
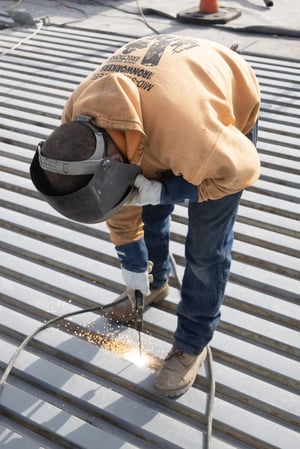
Repairing a metal roof begins with a comprehensive inspection from an objective third-party roofing consultant like Benchmark.
Their insurance company gave them an offer to tear off the roof and replace it with the same roof and amount of insulation. The company’s owner decided to get a second opinion and contacted Benchmark.
The original roof was a ribbed roof with exposed fasteners with approximately R-5 insulation. Benchmark’s experts inspected the roof and reviewed the insurance policy. The policy required that any repairs must bring the roof up to current code compliance. The current energy code called for an R-30 continuous insulation value, which is not attainable with an exposed fastener ribbed metal roof. The roof would need to be either torn off and replaced with additional insulation installed inside the buildings under the roofs or overlaid with a standing seam metal roof with the required amount of insulation. The overlay roof option was less costly, less disruptive to the business operations, and the weight of the roof overlay was less than the additional dead load allowed by the building code.
The insurance company had offered $421,742 to replace the roofs, but a code-compliant roof would cost almost twice that amount. Benchmark experts wrote a report on all the code requirements and produced a bid specification that allowed the company to solicit bids for a new roof that met the insurance policy and building code requirements.
The insurance company ended up paying for the entire new overlay roof, saving the company from accepting a solution that did not comply with their insurance policy and building code requirements. Benchmark’s approach provided the company with peace of mind, knowing that the new roof was up to code.
Whether a business is local, regional, national or global, a leaking metal roof can disrupt production, damage inventory, cause safety issues and threaten the life span of the building. Repairs should be taken seriously, beginning with an inspection by an objective third-party roof consultant like Benchmark that does not provide construction or repair services.